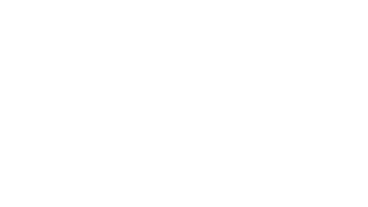
- Data inizio
- Durata
- Formato
- Lingua
- 5 Mag 2025
- 9 giorni
- Class
- Italiano
Affrontare le sfide attuali della funzione HR a 360 gradi, grazie a strumenti metodologici per attrarre, scegliere e trattenere in azienda i migliori talenti.
Volatilità e imprevedibilità sono due tra i principali aspetti che contraddistinguono gli attuali mercati. La pandemia globale è sicuramente il maggior acceleratore di questi due fenomeni ma di certo non è l’unica causa. Eventi disruptive, difficilmente prevedibili e quantificabili, sembrano essere la normalità più che l’eccezione: improvvisi shortage di materie prime, servizi logistici e capacità produttive, fluttuazioni del prezzo del petrolio repentine e difficilmente prevedibili, eventi climatici catastrofici sempre più frequenti anche in aree tradizionalmente non colpite, nuovi dazi e barriere doganali, cambi legislativi e fenomeni geo-politici più in generale sono solo altri esempi di tali eventi.
Inoltre, i mercati hanno subito profondi cambiamenti a seguito della crescente personalizzazione di prodotti e servizi. Le cause sono da ritrovarsi sia lato domanda sia lato offerta: clienti sempre più esigenti e diversi e aziende sempre più alla ricerca di nicchie di mercato non ancora esplorate; tecnologie sempre più evolute a supporto sia dell’innovazione sia delle modalità di acquisto internet-based rappresenano altri driver di questo cambiamento. Le conseguenze in termini di prodotto/servizio sono semplici: alta personalizzazione, alto mix e volumi di prodotto bassi e altamente variabili.
Sulla base di queste premesse è normale porsi la seguente domanda: «In questo nuovo contesto, qual è il migliore modello manageriale per gestire le operations e la supply chain, sia nell’industria sia nei servizi?».
Fino a oggi il modello d’eccellenza in questi ambiti è stato senza dubbio quello del LEAN management che trae origine, più di mezzo secolo fa, dal modello TPS (Toyota Production System) della Toyota.
La LEAN fonda le sue origini sulla riduzione dei muda (gli sprechi), e cioè tutte quelle «attività per le quali il cliente non è disposto a pagare». Partendo da un obiettivo di pura efficienza, le implementazioni di successo del LEAN management in aziende anche lontane dall’automotive hanno però portato risultati strabilianti, dell’ordine di svariati punti percentuali in termini di qualità, livello di servizio, puntualità e velocità. Alcune aziende hanno scelto questo percorso perché rappresentava l’ultima chance di salvezza prima del fallimento: è il caso di Porsche nel 1994 e di Ducati nel 1996.
A livello applicativo, il LEAN management si basa su due pilastri: tool e people. I tool comprendono diversi strumenti manageriali in svariati ambiti (produzione, logistica, qualità, manutenzione, gestione dei fornitori, sviluppo prodotto ecc.) da applicare con costanza e rigore. Il pilastro people, come sempre il più delicato, è costituito da diversi approcci organizzativi, a livello sia di team sia di singolo individuo, legati ai concetti di kaizen (miglioramento continuo), approccio bottom-up, empowerment, polivalenza ecc. Infine, sappiamo che il LEAN management è una filosofia manageriale che, se applicata a tutto tondo per portare miglioramenti radicali di lungo termine, coinvolge non solo gli ambiti produttivi e la supply chain ma anche lo sviluppo prodotto, il commerciale, i processi amministrativi, e, di base, tutta l’azienda.
Dunque, tutto fantastico! Perché porsi domande e dubbi? Il motivo è che nei mercati del XXI secolo alcuni di questi tool e principi di base del LEAN management sono andati in crisi perché il modello LEAN funziona meglio in condizioni di stabilità. Per esempio l’alta variabilità della domanda richiede una frequente revisione del takt time (“il ritmo della domanda”), che a sua volta implica complesse attività di re-layout e riorganizzazione del lavoro. In secondo luogo, l’alta personalizzazione del prodotto rappresenta un ostacolo per la standardizzazione del lavoro che richiede dei tempi ciclo di lavorazione che siano nell’ordine di qualche minuto. Inoltre, il livellamento della produzione (heijunka) implica l’introduzione di un periodo di pianificazione “congelato” che rende il sistema meno reattivo e flessibile.
Nonostante il LEAN management rappresenti ancora il modello d’eccellenza nelle operations e nella supply chain, questo presenta diverse vulnerabilità nel contesto attuale. È dunque naturale chiedersi che cosa fare e come intervenire. La risposta è semplice nella teoria, meno nella pratica: adottare modelli manageriali più AGILE mantenendo, dove possibile, gli elementi positivi della LEAN.
Una possibile soluzione è rappresentata dal QRM (Quick Response Manufacturing), modello sviluppato alla fine degli anni Ottanta. Tale filosofia manageriale è molto semplice nella sua essenza perché pone la velocità, tramite la riduzione di tutti i LEAD time aziendali dei processi, come l’obiettivo da perseguire. Perché? Il motivo non è solo legato al fatto che i clienti hanno esigenze temporali sempre più stringenti, ma anche alla consapevolezza che se i LEAD time vengono ridotti si hanno di conseguenza benefici relativi anche ai costi, alla qualità dei prodotti, alla puntualità e alla flessibilità. Aziende caratterizzate da alta personalizzazione, come per esempio la John Deere negli Stati Uniti e la BOSCH Hinges in Olanda, hanno infatti ottenuto miglioramenti radicali su svariate performance, non solo in termini di LEAD time, tramite un’efficace implementazione del QRM.
Oltre al superamento del tradizionale concetto di trade-off tra i vari aspetti di costo, qualità, velocità e flessibilità, il QRM scardina anche la tradizionale convinzione che la riduzione dei LEAD time sia difficile e costosa. Le regole per la riduzione dei LEAD time sono invece semplici e poco onerose: riduzione dei lotti di produzione tramite la riduzione dei set-up; pianificazione di una parte (10-20 per cento) di capacità libera (slack capacity); riduzione della variabilità dei processi interni. Mentre la riduzione dei lotti e della variabilità sono prassi note e comuni, sono poche le aziende che pianificano mantenendo una parte della capacità produttiva libera. Un motivo risiede spesso nella presenza di sistemi di cost accounting orientati al puro costo di produzione tramite la massimizzazione dell’utilizzo delle risorse, incapaci di quantificare i costi totali di supply chain e di rilevare i benefici della riduzione dei LEAD time ma solo dei tempi ciclo della produzione. Zara, nota azienda nel modo del fashion che eccelle nella gestione dei processi, è un bell’esempio di questa eccezione.
Nonostante le radici siano comuni, le differenze tra LEAN e QRM vanno al di là dell’ambito di applicazione (prodotti più standard con volumi ripetitivi per il LEAN vs prodotti custom con volumi bassi e variabili per il QRM) e degli obiettivi (riduzione degli sprechi per il LEAN vs riduzione dei LEAD time per il QRM) e abbracciano ambiti più o meno tecnici quali i layout, la gestione dei materiali e della capacità produttiva, la gestione dei fornitori e della supply chain e i sistemi di controllo di gestione. Queste differenze posizionano il QRM come un’ottima evoluzione della LEAN, e modello utile per affrontare le trasformazioni dei mercati del XXI secolo.
Ma allora, se il QRM presenta tutti questi vantaggi, si adatta meglio al contesto attuale e in gran parte dei casi è pure facile da implementare senza particolari investimenti, perché non è già adottato in larga scala? Le ragioni sono molteplici.
Il primo aspetto è di puro marketing: mentre dietro il LEAN management c’è un mondo fatto di libri, convegni, consulenti e dove svetta la Toyota, dietro il QRM c’è qualche centro di ricerca, meno libri e consulenti e aziende ancora poco numerose, di media dimensione e principalmente localizzate negli Stati Uniti.
Un secondo aspetto è legato al fatto che il QRM sradica alcuni concetti tradizionali e ben consolidati nel mondo delle operations, quali il massimo utilizzo e sfruttamento dei macchinari e della capacità produttiva, l’abbandono di obiettivi di puntualità a favore della velocità, la riduzione di approcci speculativi nelle vendite e negli acquisti e la presa di coscienza che la riduzione del LEAD time non richieda necessariamente investimenti, ma un cambio culturale di mindset.
Infine, sistemi di cost accouting e rewarding tradizionali, più orientati al costo di produzione che alla riduzione del LEAD time e del total supply chain cost, sono un ostacolo per il QRM, anche se esistono strumenti e approcci innovativi che permetterebbero di superarne i limiti.
Nonostante questi aspetti rappresentino svariate barriere difficili da abbattere velocemente soprattutto in ambiti tradizionalmente poco orientati al cambiamento come quelli delle operations, sono pienamente convinto che i cambiamenti di contesto attualmente in atto, accelerati dalla pandemia, costringeranno le aziende a essere più coraggiose e veloci nel ripensare ai propri modelli nelle operations e nella supply chain adottando modelli manageriali più agili e flessibili come per esempio il QRM.