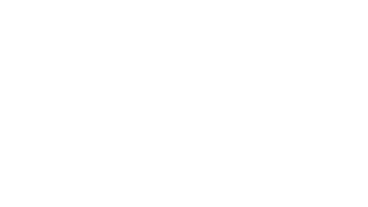
- Start date
- Duration
- Format
- Language
- 5 May 2025
- 9 days
- Class
- Italian
Affrontare le sfide attuali della funzione HR a 360 gradi, grazie a strumenti metodologici per attrarre, scegliere e trattenere in azienda i migliori talenti.
Volatile and unpredictable: these are the two main descriptors of today’s markets. The global pandemic is without a doubt the main accelerator of these phenomena, but certainly not the only driver. Disruptive events, which are hard to predict or quantify, seem to be the rule instead of the exception. These include sudden shortages of raw materials or logistical services or production capacity; abrupt price fluctuations in crude oil that are not easy to anticipate; ever-more frequent climate catastrophes, even in areas that don’t normally see similar disasters; new tariffs and trade barriers; legislative amendments and geo-political phenomena in general.
What’s more, the markets have experienced profound changes following the intense proliferation of product/service personalization. The causes behind this trend can be traced to both supply and demand. On one hand, customers are becoming more and more diverse and demanding. On the other, companies are seeking as-yet unexplored market niches and technologies are constantly evolving to support both innovation and internet-based buying. All these represent additional drivers of market change. The consequences in terms of products/services are simple: high personalization, high product/service mix and low but extremely variable product volumes.
In light of all this, it’s only natural to ask the following question: “In this new context, what’s the best model for managing operations and the supply chain, both in industry and services?”
Until today, the undisputed gold standard in these contexts was LEAN management, which emerged more than half a century ago from Toyota’s TPS model (Toyota Production System).
LEAN was founded on the concept of reducing muda (waste), that is, “all activities that the customer is not willing to pay for.” Grounded in the goal of pure efficiency, successful implementations of LEAN management in companies far afield from the automobile industry have produced amazing results, the equivalent of upticks of several percentage points in terms of improvements in quality, service level, just-in-time and speed. Some companies, such as Porsche in 1994 and Ducati in 1996, chose this path as a last resort before bankruptcy.
As far as method application, LEAN management is built on two pillars: tools and people. The first consist of managerial tools to be applied with consistency and discipline in a variety of areas: (production, logistics, quality, maintenance, supplier management, product development, etc.). The people pillar, as always, is the more delicate one. It involves diverse organizational approaches, at both a team level and an individual level, linked to the concepts of kaizen (continual improvement), bottom-up, empowerment, versatility, etc. Last of all, as we know, LEAN management is a business philosophy that impacts not only production areas and the supply chain, but also product development, the commercial function, administration processes, and basically the entire company, if it is implemented in a comprehensive way in order to enact radical, long-term improvements.
So, if everything works so well, why would we have any questions or doubts? The reason is that in 21st century markets, some of the tools and basic principles of LEAN management are breaking down because this model works best under stable conditions. For example, extreme variability in demand means companies must frequently revise takt time (“the rhythm of demand”), which in turn entails complex activities such as re-layout and re-organization of work processes. Second, the high degree of product personalization impedes work standardization, which requires processing cycles in the range of just a few minutes. In addition, levelling out the workload (heijunka) means introducing a “frozen” planning period that makes the system less reactive and flexible.
Despite the fact that LEAN management still represents a benchmark for operations and supply chain management, it’s presenting a number of vulnerabilities in the current context. So, it’s only natural to be asking what to do and how to intervene. The answer is simple in theory, but less so in practice: adopt more AGILE managerial models while maintaining the positive elements of LEAN wherever possible.
One possible solution is Quick Response Manufacturing (QRM), a model developed in the late 1980s. This business philosophy is essentially very simple: it’s all about speed, that is, gaining speed by cutting all the lead times of all company processes. Why? The reason is not just that customers want their needs met faster and faster. Companies also know that reducing lead times generates benefits relating to costs, product quality, punctuality and flexibility. In fact, organizations that offer a high degree of personalization, such as John Deere in the US and BOSCH Hinges in the Netherlands, have realized radical improvements on several performance metrics (and not only in terms of lead times) by effectively implementing QRM.
In addition to moving beyond the traditional concept of trade-offs between cost, quality, speed and flexibility, QRM is also dismantling the age-old conviction that shrinking lead times is something that’s difficult and expensive to do. Instead, the rules are simple, and actually don’t take too much effort: making production batches smaller by reducing set-ups; planning for slack capacity (keeping 10%-20% of production capacity free); minimizing variability in internal processes. It’s true that creating smaller batches and lessening variability are commonplace, familiar interventions, but only a few companies actually plan for slack production capacity. One reason often lies in cost accounting systems that calculate pure production cost based on maximizing resource utilization. But these systems are incapable of quantifying total supply chain costs, or the benefits of reducing LEAD times - they only reveal the advantages of compressing production cycle times. Zara is a well-known fashion company that excels in process management and represents an excellent example of this exception.
Despite their common roots, the differences between LEAN and QRM go beyond spheres of application (more standard products with repetitive volumes with LEAN vs custom products with low/variable volumes for QRM) and objectives (reducing waste for LEAN vs reducing LEAD times with QRM). In fact, dissimilarities also encompass more or less technical aspects such as layout, the handling of materials and production capacity, management of suppliers and supply chains, and management control systems. In light of all this, QRM is positioned as an outstanding evolution of LEAN, and a useful model for facing the transformations in today’s markets.
So if QRM offers all these advantages, if it’s a better fit for the current context, and if in most cases it’s also easy to implement, without needing major investments, why isn’t this approach being adopted on a broad scale? There are a number of reasons.
The first is pure marketing: LEAN management is a world unto itself, populated by books, conventions, and consultants, where Toyota reigns supreme. But behind QRM we only find a few research hubs, even fewer books and consultants, and so far not many companies are using it (mainly medium-sized businesses located in the United States).
The second aspect ties into the fact that QRM upends certain traditional tenets in the field of operations. These include exploiting machinery and production capacity to the maximum, sacrificing just-in-time in favor of speed, minimizing speculative approaches in sales and purchasing. What’s more, organizations have to realize that cutting lead times does not necessarily require investments, but does call for a cultural change in mindset.
Finally, traditional cost accounting and rewarding systems, which focus more on production costs rather than total supply chain costs or shortening lead times, represent obstacles for QRM. (That said, there are innovative tools and approaches that would enable companies to contend with them.)
So yes, there are barriers that would be hard to overcome quickly, in particular in areas that traditionally have little inclination for doing things differently, such as operations. But despite this, I am fully convinced that the changes that are currently underway, changes that are accelerating due to the pandemic, will force companies to be faster - and braver - in rethinking their operations and supply chain models, and adopting more agile and flexible managerial models such as, for example, QRM.